Introduction
Diesel generators play a crucial role in providing backup power during emergencies and ensuring continuous operations in various industries. One important aspect of diesel generators is their durability, which is essential for ensuring reliable performance over an extended period of time. Durability testing is a critical process that helps manufacturers evaluate the robustness and longevity of diesel generators under different operating conditions. In this article, we will delve into the importance of durability testing for diesel generators, the key factors that influence their durability, and the various testing methods employed to assess their performance.
Importance of Durability Testing for Diesel Generators
Durability testing is a vital aspect of the product development process for diesel generators. It allows manufacturers to assess the performance and reliability of their products under real-world conditions and identify any potential weaknesses that need to be addressed. By subjecting diesel generators to rigorous testing, manufacturers can ensure that their products meet industry standards and customer expectations for durability and longevity.
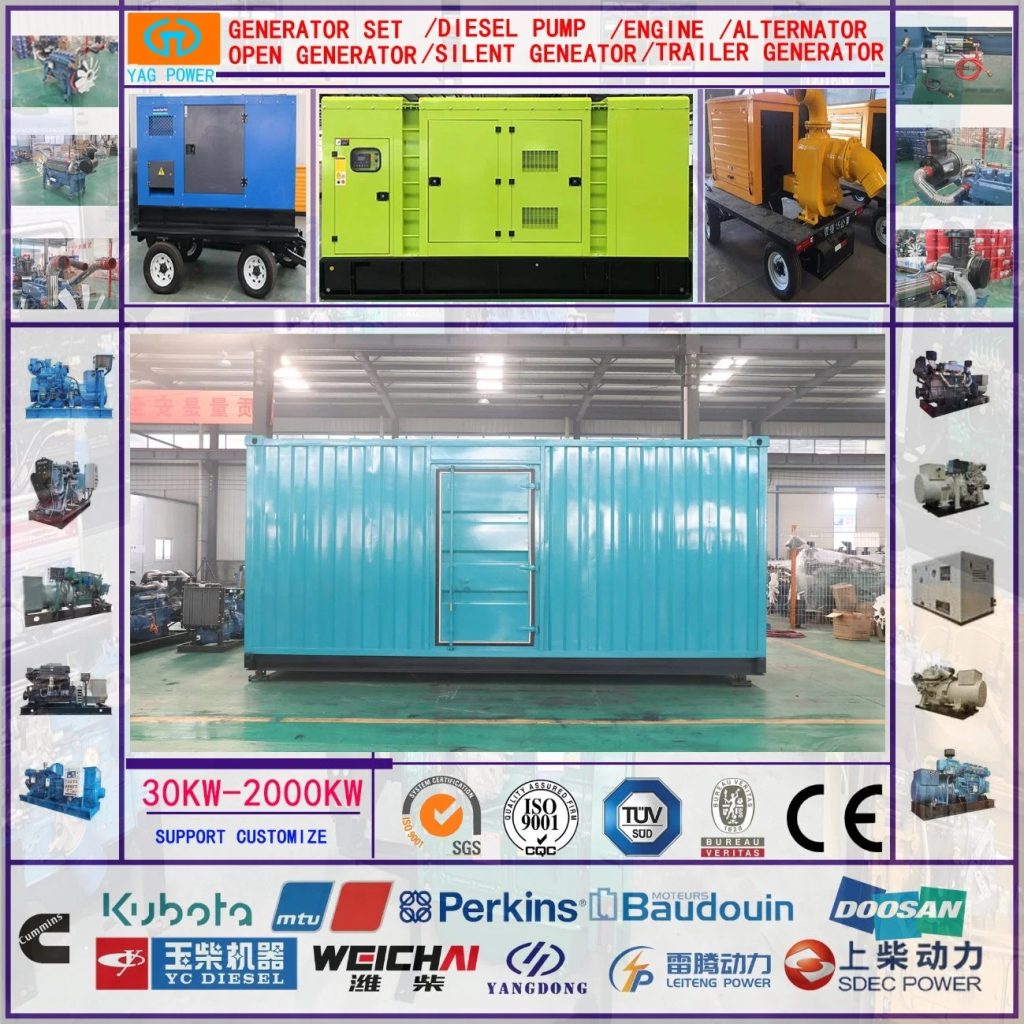
One of the primary reasons why durability testing is essential for diesel generators is to verify their ability to withstand the rigors of continuous operation. Diesel generators are often used as backup power sources in critical applications such as hospitals, data centers, and industrial facilities. In these environments, the reliability of the generator is paramount, as any downtime can result in significant financial losses or even jeopardize human lives. Durability testing helps manufacturers simulate the demanding conditions that diesel generators may encounter in the field, allowing them to identify potential issues and make necessary design improvements.
Furthermore, durability testing also helps manufacturers validate the quality of materials and components used in the construction of diesel generators. By subjecting the generator to various stress tests, such as thermal cycling, vibration testing, and load testing, manufacturers can assess the performance of critical components like the engine, alternator, and cooling system. This enables them to identify weak points in the design and make modifications to enhance the overall durability and reliability of the generator.
Key Factors Influencing Durability of Diesel Generators
Several factors can influence the durability of diesel generators, ranging from design considerations to operational parameters. Understanding these factors is essential for manufacturers to develop robust and long-lasting products that can meet the demands of diverse applications. Some of the key factors that influence the durability of diesel generators include:
1. Design and Construction: The design and construction of a diesel generator play a significant role in determining its durability. Factors such as the choice of materials, structural integrity, and component layout can impact the generator's ability to withstand environmental conditions, mechanical stress, and operational loads. A well-designed generator with robust construction is more likely to exhibit superior durability compared to one with subpar design and construction.
2. Engine Performance: The engine is the heart of a diesel generator and plays a critical role in determining its overall performance and longevity. Factors such as engine design, power output, fuel efficiency, and maintenance requirements can influence the durability of the generator. A high-quality engine with a proven track record of reliability is essential for ensuring the long-term durability of the generator.
3. Cooling System: The cooling system of a diesel generator is responsible for dissipating heat generated during operation and maintaining optimal operating temperatures. An efficient cooling system is essential for preventing overheating and ensuring the longevity of critical components such as the engine and alternator. Factors such as cooling capacity, airflow design, and maintenance requirements can impact the durability of the generator.
4. Electrical Components: The electrical components of a diesel generator, including the alternator, control panel, and wiring harness, are crucial for its overall performance and reliability. Factors such as component quality, insulation resistance, and voltage regulation can influence the durability of the generator. Proper selection and testing of electrical components are essential for ensuring the long-term reliability of the generator.
5. Environmental Conditions: The operating environment in which a diesel generator is deployed can have a significant impact on its durability. Factors such as temperature extremes, humidity levels, dust and debris, and exposure to corrosive agents can affect the performance and longevity of the generator. Manufacturers must consider these environmental factors during the design and testing phase to ensure that the generator can operate effectively in challenging conditions.
Durability Testing Methods for Diesel Generators
Durability testing for diesel generators involves subjecting the generator to a series of tests and evaluations to assess its performance and reliability under different conditions. Various testing methods are employed to simulate real-world scenarios and identify any potential weaknesses in the design or construction of the generator. Some of the common durability testing methods for diesel generators include:
1. Thermal Cycling Test: The thermal cycling test involves subjecting the diesel generator to rapid temperature changes to simulate the effects of thermal stress on critical components. By exposing the generator to alternating high and low temperatures, manufacturers can evaluate its ability to withstand thermal expansion and contraction without compromising performance or reliability. This test helps identify potential issues such as material fatigue, solder joint failures, and thermal cycling-induced stress.
2. Vibration Testing: Vibration testing is used to assess the structural integrity and mechanical robustness of a diesel generator under dynamic loads. By subjecting the generator to controlled vibrations at varying frequencies and amplitudes, manufacturers can identify any weak points in the design that may lead to premature failure or reduced durability. 500kw diesel generator for oil and gas facilities helps evaluate the resilience of components such as engine mounts, alternator bearings, and electrical connections to ensure they can withstand the rigors of continuous operation.
3. Load Testing: Load testing involves applying varying electrical loads to the diesel generator to evaluate its performance under different operating conditions. By simulating real-world load profiles and monitoring key parameters such as voltage regulation, frequency stability, and power output, manufacturers can assess the generator's ability to deliver consistent and reliable power. Load testing helps identify any issues related to engine response, voltage drop, or overload protection that may affect the durability of the generator under heavy loads.
4. Environmental Testing: Environmental testing is conducted to assess the performance of a diesel generator in different environmental conditions, such as temperature extremes, humidity levels, and exposure to dust and debris. By subjecting the generator to harsh environmental conditions, manufacturers can evaluate its ability to maintain optimal performance and reliability. Environmental testing helps identify potential issues such as corrosion, condensation, and thermal stress that may impact the durability of the generator in real-world applications.
5. Endurance Testing: Endurance testing involves running the diesel generator continuously for an extended period of time to evaluate its long-term performance and reliability. By subjecting the generator to continuous operation under full load conditions, manufacturers can assess its ability to withstand prolonged use without experiencing failures or performance degradation. Endurance testing helps validate the overall durability of the generator and identify any issues related to overheating, wear and tear, or component fatigue that may affect its longevity.
Conclusion
Durability testing is a critical aspect of ensuring the reliability and longevity of diesel generators in various applications. By subjecting generators to rigorous testing under different conditions, manufacturers can identify potential weaknesses in design and construction, validate the quality of materials and components, and ensure that their products meet industry standards and customer expectations for durability. Understanding the key factors that influence the durability of diesel generators, such as design considerations, engine performance, cooling systems, electrical components, and environmental conditions, is essential for developing robust and long-lasting products. Employing a range of durability testing methods, including thermal cycling, vibration testing, load testing, environmental testing, and endurance testing, helps manufacturers evaluate the performance and reliability of diesel generators under real-world conditions and deliver products that can withstand the rigors of continuous operation. By prioritizing durability testing as part of the product development process, manufacturers can ensure that their diesel generators meet the highest standards of quality, reliability, and durability.